Eine Großsegler mit Klapptriebwerk hat schon was. Doch Optik und Aerodynamik sind nicht alles, wie Wolfgang Mache bei seiner 8,4 Meter spannenden ASH 31 feststellen musste. Der durch den Ausfahrvorgang des Triebwerks um einige Sekunden verzögerte Motoranlauf erlaubt beispielsweise kein spontanes Durchstarten, wenn die Landeeinteilung mal nicht ganz optimal war. Also wurde eine praxisfreundlichere FES-Variante des imposanten Modells gebaut, die er hier vorstellt.
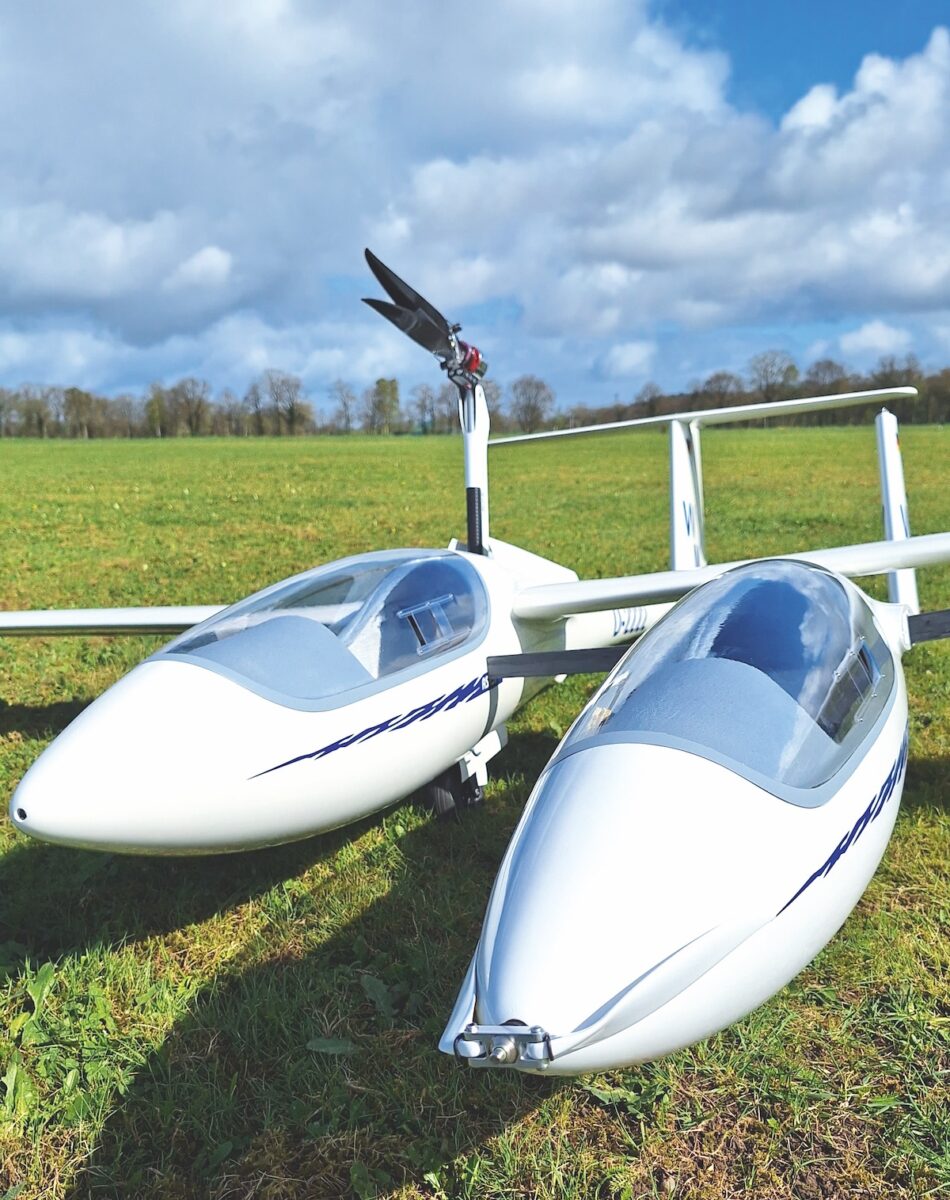
Eigentlich ein Traum: die ASH-31 mit Klapptriebwerk
Diese ASH 31 wurde bereits als Modell der Mi-Ausführung gebaut. Das bedeutet, dass im Rumpf ein Klapptriebwerk im Rücken integriert ist, mit all den Vor- und Nachteilen, die damit verbunden sind. Fliegerisch und optisch ist die Mi ein Traum; der Einsatz über zwei Flugsaisons hat jedoch einige Nachteile in der praktischen Handhabung gezeigt. Gern flog ich den großen Segler in beiden Spannweitenvarianten mit 7.200 mm und 8.400 mm und tue es auch heute noch. Es ist eine richtige Zeremonie, wenn bei der Mi-Version in der Startposition ein Schalter umgelegt wird und die SM-Steuerung für das K25 Evo Klapptriebwerk den Startvorgang aktiviert. Alles läuft nun automatisch ab, vorausgesetzt, alle notwendigen Programmierungen der Abfolgen wurden korrekt in die SM-Steuerung eingegeben. Die Rumpfklappen öffnen sich; zwei Sensoren bestätigen den Abschluss des Fahrvorgangs und das Verharren der Klappen in der Endstellung. Dies ist das Signal für das Ausfahren des Triebwerkarms, wiederum bis zur Endstellung, bestätigt durch einen weiteren Sensor. Erst dann wird der Impuls zum Motoranlauf gegeben. Der Motor fährt nach einer einprogrammierten Gaskurve langsam hoch, das Modell beschleunigt und hebt schließlich ab. Alles wirkt einfach für den Zuschauer, und eigentlich ist es das auch. Doch die Programmierung des Ganzen erforderte etliche Stunden des Tüftelns, Probierens und Justierens.
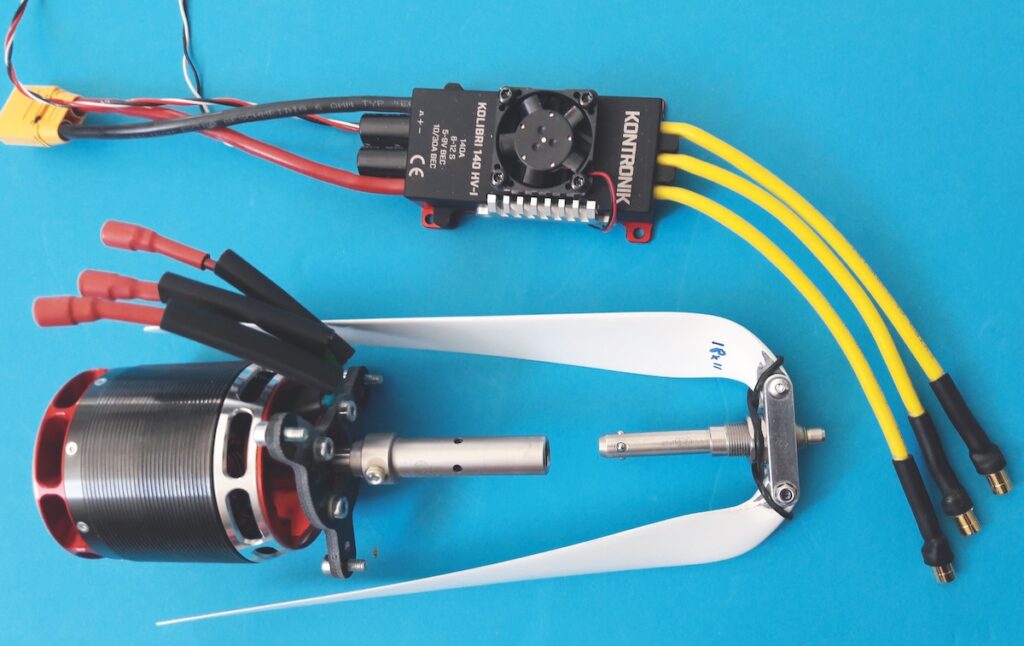
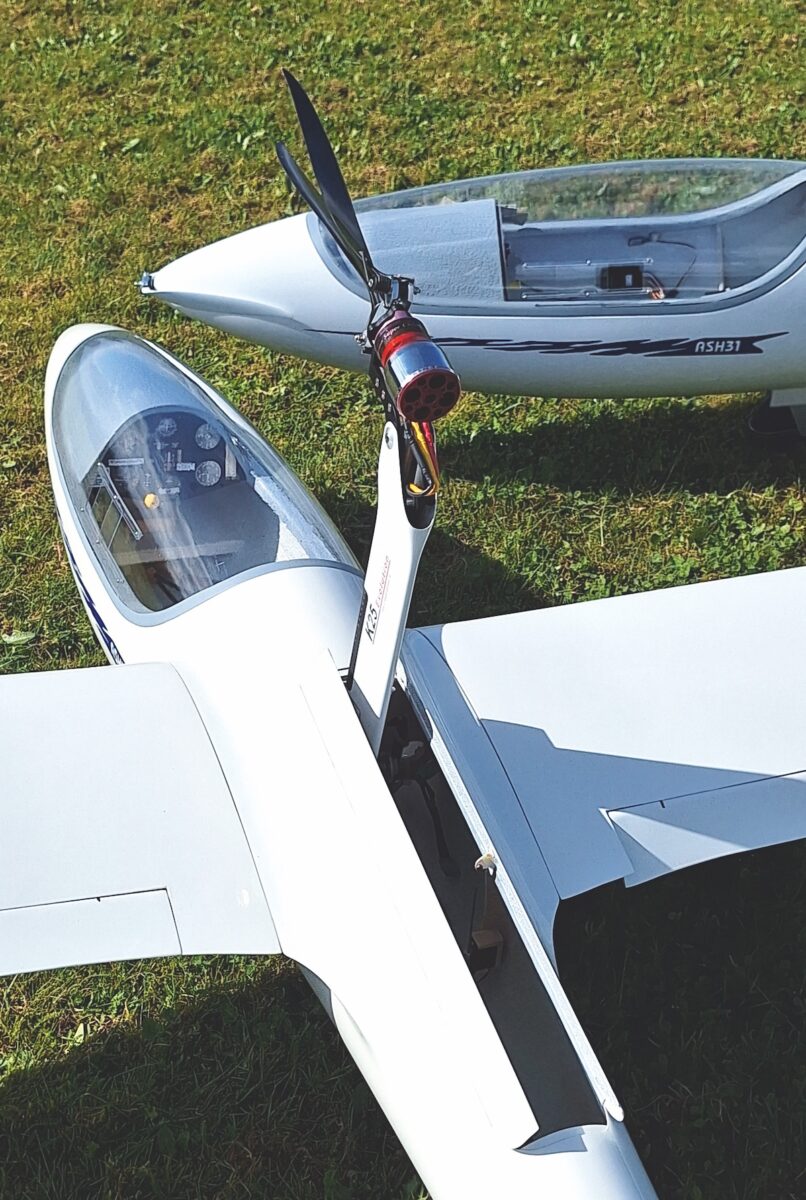
Der Einfahrvorgang läuft ebenso unproblematisch ab; jede einzelne Aktion wird durch Sensoren bestätigt, ehe die nächste eingeleitet wird. Dann gleitet der Segler wie das Original, ohne dass die Optik oder die Aerodynamik durch den Antrieb gestört werden. Alles gut also? Eigentlich ja, wenn da nicht die Landungen mit diesem Dickschiff wären. Diese sind nicht problematisch, aber im Notfall möchte ich die Möglichkeit haben, etwas Gas nachzuschieben, wenn der Anflug zu kurz erscheint. Oder auch aus Sicherheitsgründen durchstarten zu können, wenn zu hoch angeflogen wurde oder ein Hindernis auf der Bahn erscheint. Grundsätzlich ist das auch mit dem Klapptriebwerk möglich, aber die Zeitspanne von der Entscheidung zum Durchstarten bis zur tatsächlichen Gasannahme und der folgenden Beschleunigung ist bei einem solchen Klappsystem enorm. Der Vorgang bis zum Hochlaufen des Motors benötigt locker 7 – 8 Sekunden, was endlos lang erscheint, wenn man die Power sofort benötigt. Man könnte dies umgehen, indem das Triebwerk zur Landung grundsätzlich ausgefahren bleibt und der Motor über einen zusätzlichen Kanal angesteuert wird. Damit wäre jedoch der Vorteil des »Ein-Schalter-Systems« von SM-Modellbau dahin. Außerdem ist die Landung mit ausgefahrenem Klapparm nicht nur optisch unschön, sondern die Belastung ist für den Triebwerksarm und die gesamte Mechanik bei möglichen Schiebelandungen und Querbeschleunigungen hoch.
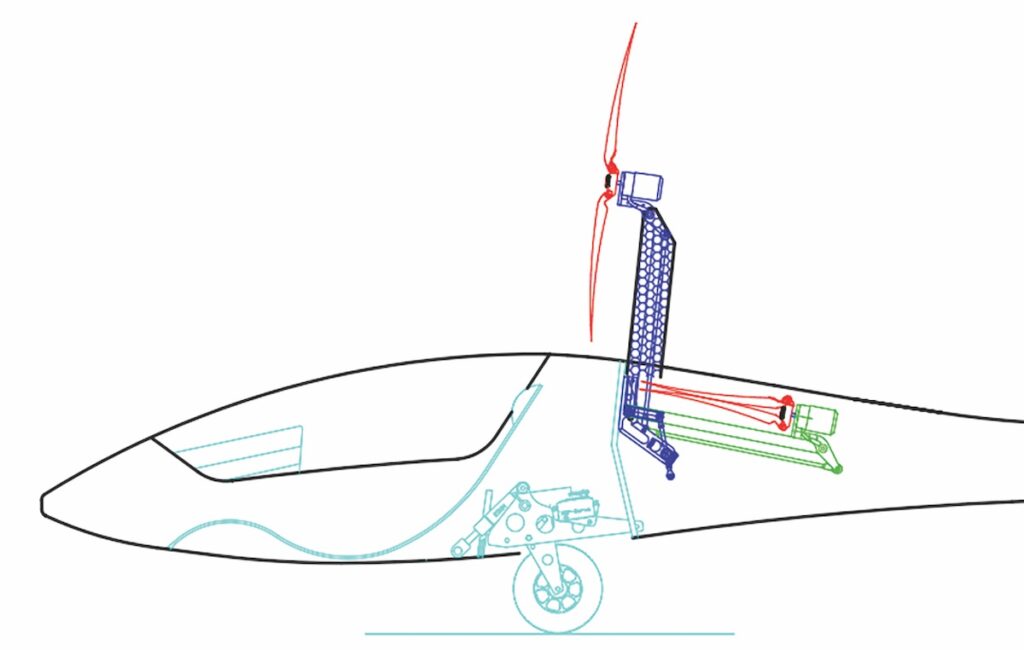
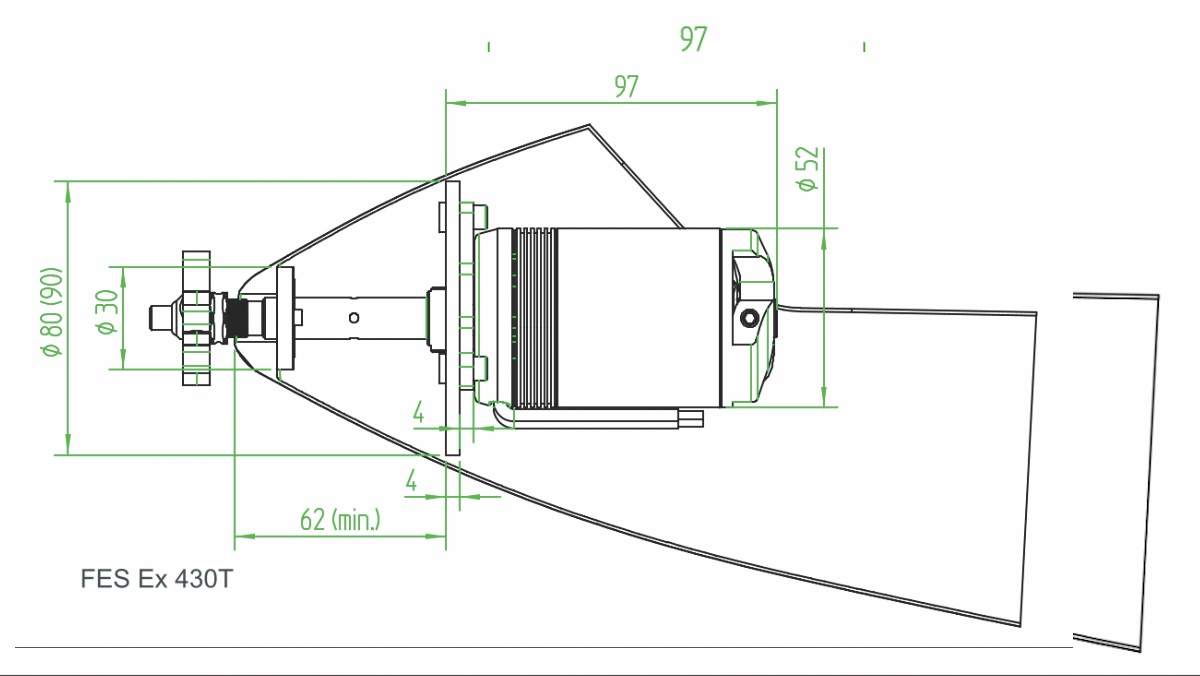
FES ist die Lösung
Was könnte also die Lösung des Problems sein, denn ein Antrieb sollte in jedem Fall in das Modell? Richtig: der FES-Antrieb. Meiner Meinung nach ist er der perfekte Kompromiss aus Praxisnähe und Sicherheit im Flugbetrieb. Aerodynamisch ist er sicherlich nicht das Optimum und optisch auch nicht ideal, aber dafür gibt es eine Lösung. Aus der ersten Idee, das bestehende Modell einfach mal so eben schnell umzurüsten, wurde natürlich nichts. Deshalb fiel die Entscheidung, ein komplett neues Modell dieses Typs aufzubauen und es dann mit dem FES-Antrieb zu versehen. Das war keine große Herausforderung, denn schließlich handelt es sich um eine eigene Konstruktion, die mein Freund Klaus Dräger (ehemals KD-Flugmodelltechnik) zum Bausatzmodell weiterentwickelt hat. Ich nistete mich also in der Werkstatt von Klaus ein, und nach einigen Tagen war ein neuer Grundbausatz bestehend aus Sandwichtragwerk und einem GfK/CfK-Rumpf fertig. Das Tragwerk wurde genauso aufgebaut wie unsere erste Version: durchgehender, beschichteter Sandwichholm, komplette Belegung mit abgestuften Kohlegewebelagen, Hohlkehlenanschlag der Ruder, Integration von Schambeck-Störklappen, 2K-Lackierung usw. Warum sollte man hier von Bewährtem abweichen? Beim Rumpf war es dann aber schon etwas anders. Während beim Heck alles beim Alten blieb, wurden die Neuerungen beim Ein- und Ausbau der notwendigen Komponenten im Fahrwerksbereich, Cockpit und Nasenbereich durchgeführt.
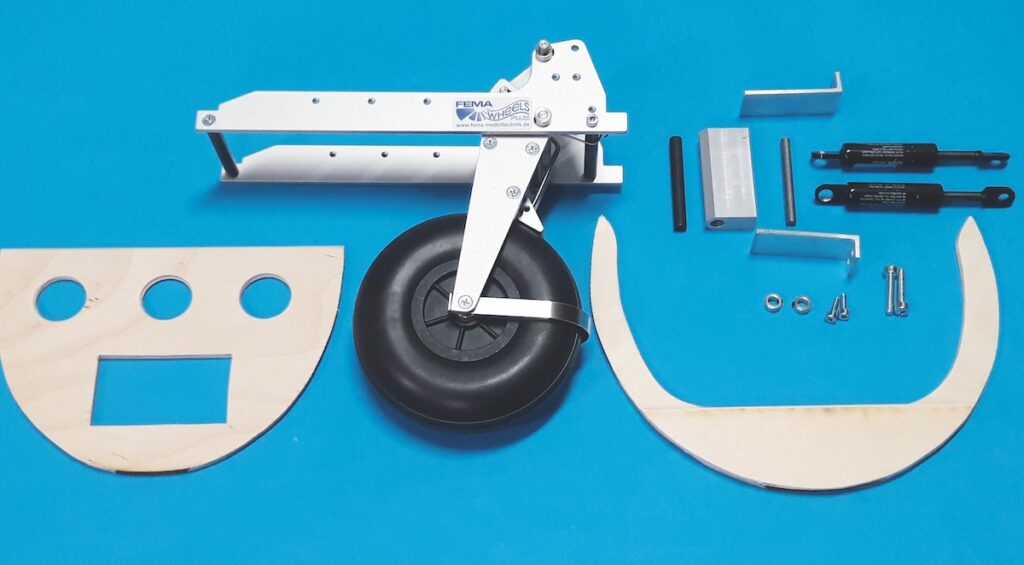
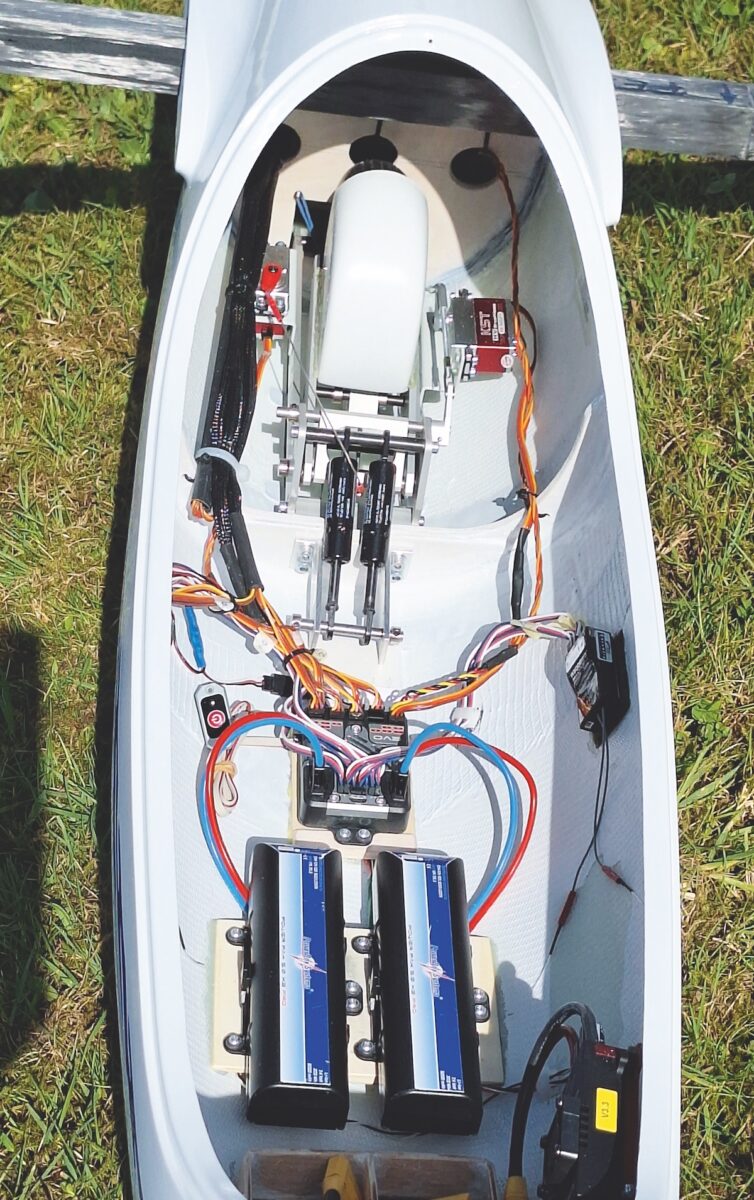
Fahrwerk
Fangen wir mit dem Fahrwerk an. Bei einem Großmodell wie diesem werden besondere Anforderungen an eine zuverlässige Funktion, eine sichere Verriegelung in den Endstellungen und eine wirksame Radbremse für »zu kurze Landebahnen« gestellt. Aufgrund des Gewichts (max. 19 kg in der 8,4 m-Version) sollte es auch über eine wirksame Dämpfung verfügen. Zudem musste es eine Version mit verlängerten Achsschenkeln sein, um die nötige Bodenfreiheit für den FES-Propeller in der Rumpfnase zu gewährleisten. All das bietet Torcman/FEMA an. Das gefederte FEMA XL FES Fahrwerk für Modelle im Maßstab von 1:2,7 bis zu 1:2 und Gewichte bis zu 35 kg ist ideal. Es ist nicht nur robust genug, sondern erhöht in der Version mit den FES-Schenkeln die Bodenfreiheit um 30 mm im Vergleich zur normalen Ausführung. In der neuesten Version wurde die Konstruktion gewichtsoptimiert, und es sind auch GfK-Radabdeckungen für die 127er Radgröße verfügbar, um Verschmutzungen im Inneren des Rumpfs durch eingewirbeltes Gras oder Erde zu vermeiden. Die Fahrwerksmechanik wird zwischen zwei stabilen Sperrholzspanten im Rumpf eingebaut. Der vordere Spant dient als Auflage für das Drehlager des Fahrwerks, an dem sich die gesamte Konstruktion abstützt. Der hintere Spant ist mit seitlichen Schlitzen versehen, die als Führung für die Seitenflanken des Fahrwerks beim Einsatz mit den Gasdruckdämpfern dienen. Diese hintere Führung ist zwar nicht zwingend nötig, aber bei Schiebelandungen als feste seitliche Begrenzung der Mechanik sinnvoll.
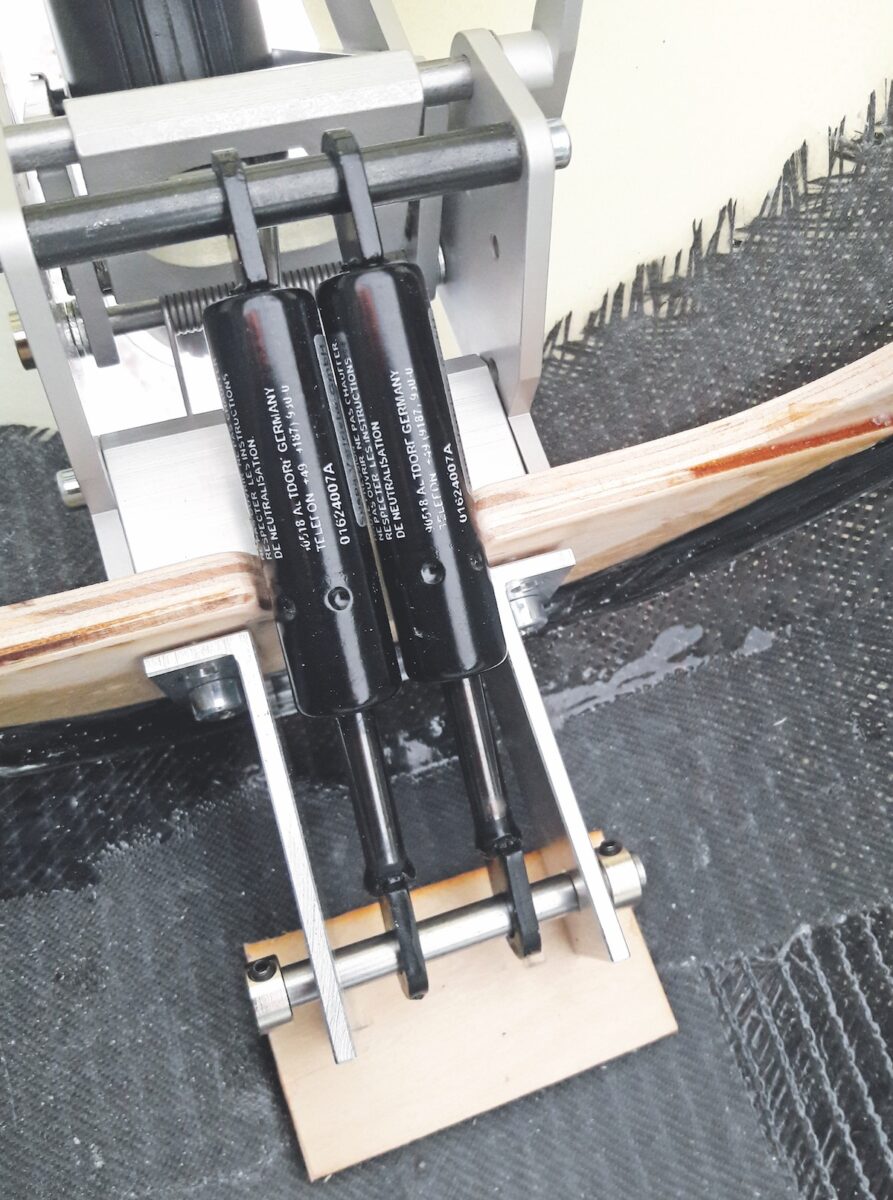
Die Fahrwerksdämpfung mittels Gasdruckdämpfern wird dem Gewicht des Modells angepasst. Die Radbremse wird von einem seitlich am beweglichen Fahrwerksrahmen angebrachten Servo betätigt, sodass sie auch beim Einfedern des Fahrwerks sicher funktioniert. Die Bremswirkung kann sehr feinfühlig dosiert werden, bis hin zur Blockade des Rades. Entsprechende Servorahmen und nötige Anlenkhebel hierfür sind im Zubehörangebot bei FEMA verfügbar. Ein sogenannter Z-Servohalter löst das Problem der schrägen Anlenkung zum Aus- und Einfahren des Einziehfahrwerks. Ein Standardservo kann mit diesem Halter liegend montiert werden, sodass Servo- und Fahrwerkshebel in einer Linie zueinander laufen. Da es sinnvoll ist, das Servo mit 180° Ausschlag zu betreiben, ist ein gewinkelter Gabelkopf die ideale Ergänzung. Ein L-Servohalter wird für die Montage eines Servos für die Radbremse angeschraubt. Und der Einbauort der Mechanik? Auf keinen Fall möchte man eine Bodenberührung des Propellers beim Beschleunigen im Startvorgang. Deshalb wird bei einem Modell mit FES-Antrieb das Fahrwerk um einige Zentimeter von der ursprünglichen Position weiter nach vorn gesetzt. Bei dieser ASH sind es 5 cm, was ungefähr der Position beim Modell mit Klapptriebwerk entspricht. Die Einbauanleitung des FEMA-Fahrwerks gibt eine gute Information zur Festlegung der Einbauposition.
Welcher FES-Antrieb soll’s werden?
Ist das Fahrwerk komplett eingebaut, geht es um die Integration des FES-Antriebs. Doch welcher soll es sein? Bei Torcman gibt es scheinbar unendliche Antriebsvorschläge für Segler. Und selbst wenn das passende Modell nicht dabei sein sollte, ruft man einfach den Fachmann vor Ort an. Firmenchef Klaus Kraft gibt immer einen guten Rat …
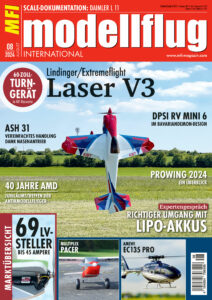